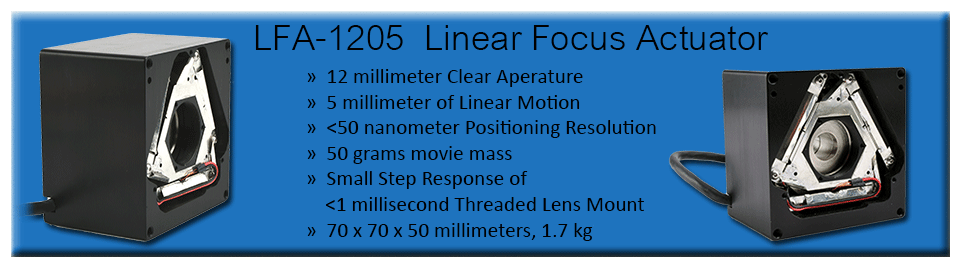
The Linear Focus Actuator is a high performance compact positioning actuator. It was specifically developed for applications requiring both high precision and high-speed positioning over a short to medium stroke. This product mates the voice coil motor to a perfectly smooth flexure guidance system and a very high resolution position feedback encoder. The LFA is well suited for optical focusing and other micro-positioning applications in markets such as semiconductor, medical, optical testing, scanning microscopy, circuit board assembly and micro manufacturing. The LFA-1205 has a 12 mm diameter clear aperture through its center, and 5mm of available stroke. Different configurations of stroke length, force constant, optic mounting, and other options are available as needed. The LFA1205 comes stock with a M26 threaded mount.
Voice Coil Motor: The motor used in the LFA is a custom designed moving coil motor optimized using advanced computer modeling. The magnets used in Equipment Solutions motors have some of the highest magnetic flux densities available. Its coil characteristics, including the resistance and inductance, were closely designed to match the capabilities of the SCA814 Servo Controlled Amplifier. The motor can drive the stage to unparalleled accelerations and peak velocities.
Flexure Stage Guidance: The LFA series uses flexures for guidance along the motion axis. Flexures provide perfectly smooth motion. When designed and used properly they can have infinite lifetime. The LFA flexure and motor configuration is symmetric about a central axis where an optic is usually mounted. The resultant optical axis is coaxial with the motion axis of the flexure and the force vector of the motor, and this axis passes through the center of mass of the moving system, thus producing no net torque. The LFA flexure is stiff in all 5 cross-axes to the motion axis, except there is a small parasitic rotation about the motion axis that is proportional to the position on the motion axis. This parasitic motion is inherent in flexure systems, but which axis is left to the choice of the designer. ESI chose the parasitic axis to be a rotation about the motion axis that doesn’t affect the intended application for most customers. Most LFAs are used in optical applications where a rotation of the optic about the optical axis is not an issue.
Position Feedback: In it’s standard configuration the LFA uses a non-contact optical analog position encoder that makes it directly compatible with the SCA814 Servo Controlled Amplifier. The 50 nanometer positioning repeatability described in the specifications section assumes this sensor technology. The analog nature of the position sensor promotes the exceptionally high positioning resolution and bandwidth. For compatibility with digital servo systems the LFA can be optionally configured with a digital quadrature encoder.
Specifications
Clear aperture (option) | 12 mm |
Range of Motion | 5 mm |
Positioning Resolution | <50 nm (analog)1mm (digital) |
Peak Force | 30 lbs (for 10 sec.) |
Max Continuous Force | 4.5 lbs (20 N) |
Motor Constant | 0.6 lbs/Amp (2.7 N/Amp) |
Coil Resistance | 1.5 ohms |
Coil Inductance | 100 mH |
Travel Non-Straightness | <0.5 um (Flexure) |
Dimension | 70 X 70 X 50 mm (600 g) |
Total Mass | 1.7 kg |
Moving Mass | 50 g |
cable length (stock) | 28” (700 mm) |
Downloads & Data Sheets
LFA-1205 Linear Focus Actuator – Presents the mechanical details necessary for integration of the product.
LFA-1205 Position Sensor Nonlinearity